K
KMS
Well-known member

This is a discussion on "grey" areas in regards to turbocharging. I answer many of the same questions every day, one at a time on many confusing subjects that really are misunderstood. I want to help, so, we will open topics to provide accurate information and explain how and why stuff works. This topic is how to ensure your turbo is well protected for the long haul.
<O
The first thing that a turbo needs is oil. Sounds simple, however, on small engines with wet clutches things can get complicated. The first area of concern is where to get the oil supply and how to regulate it.
<O
The most logical place to get oil pressure is from the oil filter galley. Pressure here will range from 30-60 psi (depending on the model). At these pressure levels, the turbo will receive too much oil….Yes, too much oil. Turbos only require between 12-20 psi of oil pressure. The excessive pressure from the oil filter galley will bleed past the oil seals on the turbo and cause smoking and carbon build up.
<O
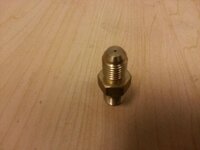
So how do you regulate the pressure? The most common way is to use a restrictor jet. This restrictor jet is most commonly located on the feed fitting to the turbo. These jets will range from .024” to .040”. The smaller the hole, the lower the pressure to the turbo. A simple and clean method, however there is a dark side…clogging!
<O
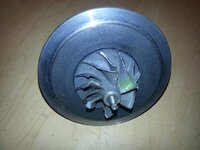
Particles from the oil system can enter this orifice and plug it. This will starve the turbo and lead to failure. So how do you prevent blockage? Answer: an inline filter. I use a simple and compact inline -3 filter that is serviceable. This works great if you are using AN fittings, however if you are using rubber hose, a small fuel injection fuel filter will do the trick. However, take note of the micron rating because there is another gremlin in the oil that must be addressed…clutch fibers.
<O
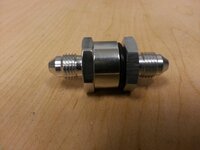
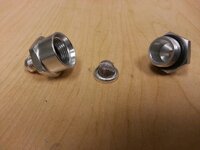
Clutch fibers are very small and will not clog restrictor jets, however they will kill the bearing system in the turbo. Clutch fibers act as a lapping compound at high velocity and will create excessive clearance on the turbo shaft and bearing system. To keep these fibers out, you must use a filter that has a micron rating lower than 40. That is small enough to keep your turbo out of harm’s way.
<O
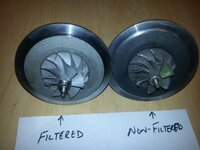
Hey, wait a minute…If we are picking up oil from the oil filter cover, is that oil not filtered? Answer: It depends on the model. For the most part, the outside of the oil filter is dirty oil and the inside of the oil filter is clean oil. If the pickup point is on the inside of the oil filter, the oil will be clean. If not, the oil is most likely straight from the sump. For example, Hondas will have clean oil at this point. Kawasaki and KTM will have dirty oil at this point. Bottom line, turbos are not cheap to replace, so if in doubt, use a filter.
<O
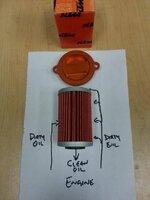
Now let’s take a look at air filtration. For snow biking, what we are trying to keep out is snow and ice. I have always used a K&N with an outerwear. The outerwear is a great line of defense and the K&N will pick up moisture that the outerwear cannot. I have seen the use of just an outerwear with a cage or net system that have worked just fine. However, I have been receiving calls from people that have used the Outerwear only system with moisture ingestion problems leading to very costly repairs. I would love to hear from the community on this, so please chime in if you can shed some light on this.
<O
Another area of protection with a sweet side is the use of a Blow off valve. The purpose of the blow off valve is to bleed off compressed air (boost) during decel…What? Get rid of boost! Why would you do such a crazy thing like that?
Answer #1: To prevent compressor surge. Under wide open throttle turbos can spin over 100,000 rpm. At some point you will have to shut the throttle to slow down or shift. The turbo is still spinning and compressed air traveling up to 400 ft/s has no where to go. The throttle plate now serves as a brick wall. The pressure builds and slams the brakes on your turbo! Turbos do not like this. They will lose almost 90% of their velocity in a fraction of a second. Because the wheels have mass, the shaft and bearing system become unstable and make all sorts of weird chirping noises. The damage will not come immediate, however given enough seasons the turbo will fail and show these very odd looking swirl marks on the bearing surfaces.
<O
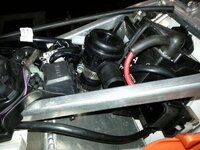
Answer #2 for the use of a blow off valve…It adds performance! How? Turbine velocity. Remember the brick wall scenario in which turbo velocity gets decimated by 90%? Well, if you give the air an exit strategy the turbo will free spin because there is very little resistance. In this case, the wheels keep spinning and the moment you get back onto the gas the turbo will be ready to serve you with boost. It will not have to go from “zero to hero” and the lag will disappear for upshifts and on/off/on throttling.
<O
Thanks for reading and questions are always appreciated.<O