Reposting some previous posts that have missing photos
Post #40
Small update in this thread about my turbo conversion:
So far, one can summarize that it works beyond expectations and look forward to the coming winter season!
Among the final rounds last spring began pushing coolant. Realised pretty quickly that I had blown the head gasket. In pic below you can clearly see where it failed. A fairly simple error to fix. Need stronger head studs.
While I still had the head off I wanted to take the opportunity to examine the comp reduction was possible.
Original gasket is more than 1 mm. Washers in the photo is 2 mm, and then the timing chain max tensioned without chain tensioner fitted. This gives the comp ratio 10,05:1. The limitation to raise the head is the timing chain length.
Mounted the head. There were two gaskets. Cylinder head gaskets are comprised of three layers. Had to remove one. Otherwise it would have been too thick and the chain is too short. The chain is stretched with the tensioner in the end position.
This fall I disasembled head, piston and cylinder. Sent them to MotoSpeed in Sweden for correct measurement of volume of the combustion chamber. They work with JE pistons who hopefully make a custom made low comp piston. There are at least 8 weeks delivery time so I'm a little late ...
Stock comp ration is 11,8:1 and I will run 10:1. This will also require race fuel but do not want to lose too much bottom end. My goal is to safely boost 10-11,5 psi with race gas or 7-8 psi with pump gas.
Measuring squish
to be continued.....
<!-- / message --><!-- edit note -->
Post #40
Small update in this thread about my turbo conversion:
So far, one can summarize that it works beyond expectations and look forward to the coming winter season!
Among the final rounds last spring began pushing coolant. Realised pretty quickly that I had blown the head gasket. In pic below you can clearly see where it failed. A fairly simple error to fix. Need stronger head studs.
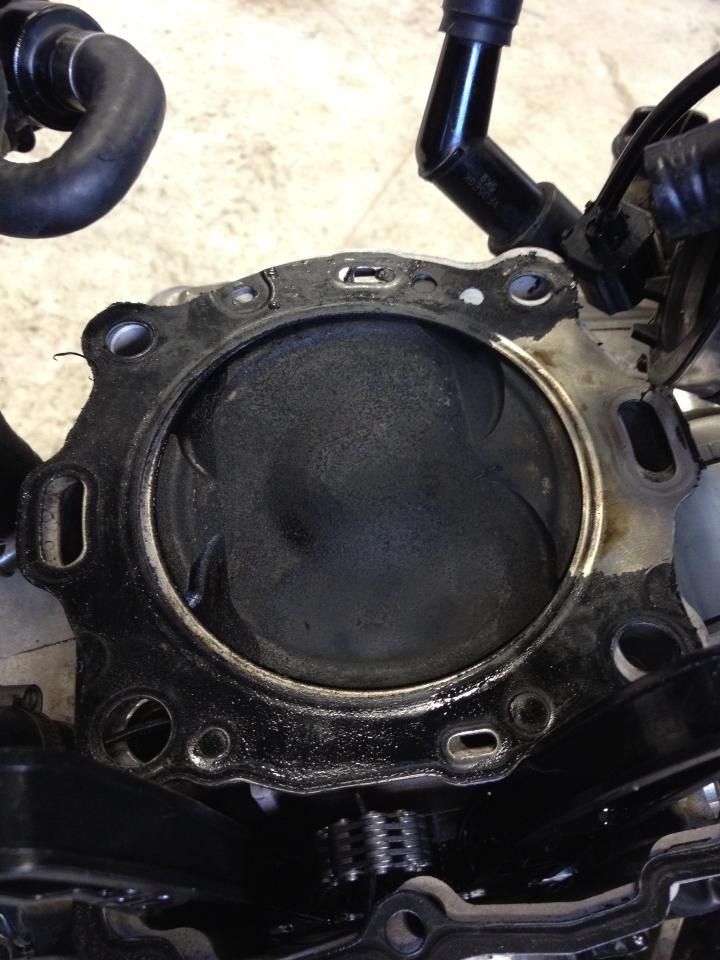
While I still had the head off I wanted to take the opportunity to examine the comp reduction was possible.
Original gasket is more than 1 mm. Washers in the photo is 2 mm, and then the timing chain max tensioned without chain tensioner fitted. This gives the comp ratio 10,05:1. The limitation to raise the head is the timing chain length.
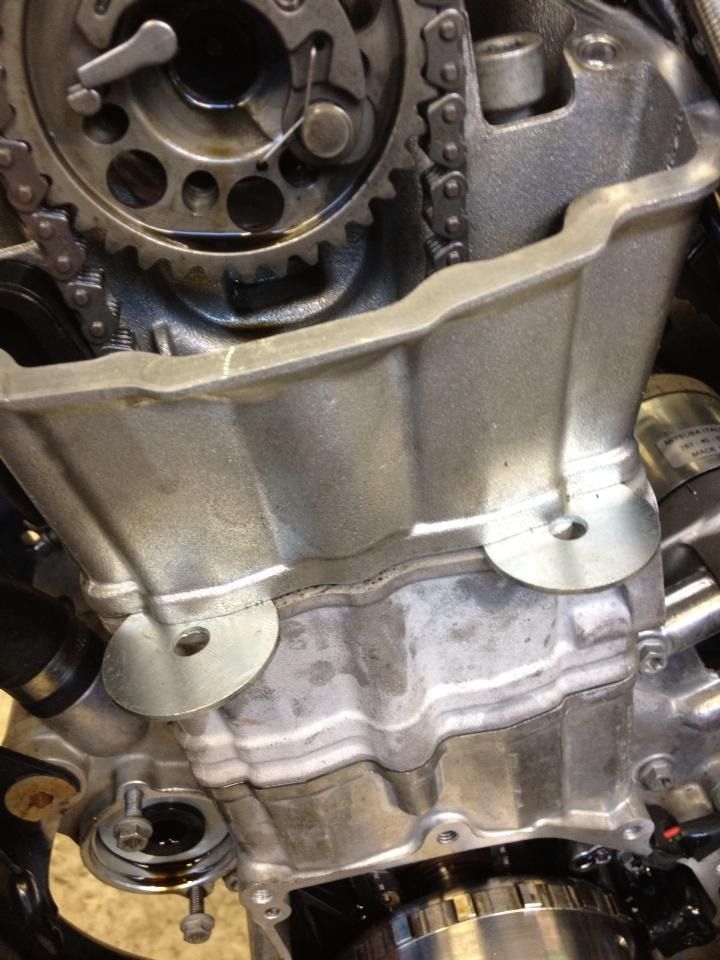
Mounted the head. There were two gaskets. Cylinder head gaskets are comprised of three layers. Had to remove one. Otherwise it would have been too thick and the chain is too short. The chain is stretched with the tensioner in the end position.
This fall I disasembled head, piston and cylinder. Sent them to MotoSpeed in Sweden for correct measurement of volume of the combustion chamber. They work with JE pistons who hopefully make a custom made low comp piston. There are at least 8 weeks delivery time so I'm a little late ...

Stock comp ration is 11,8:1 and I will run 10:1. This will also require race fuel but do not want to lose too much bottom end. My goal is to safely boost 10-11,5 psi with race gas or 7-8 psi with pump gas.

Measuring squish
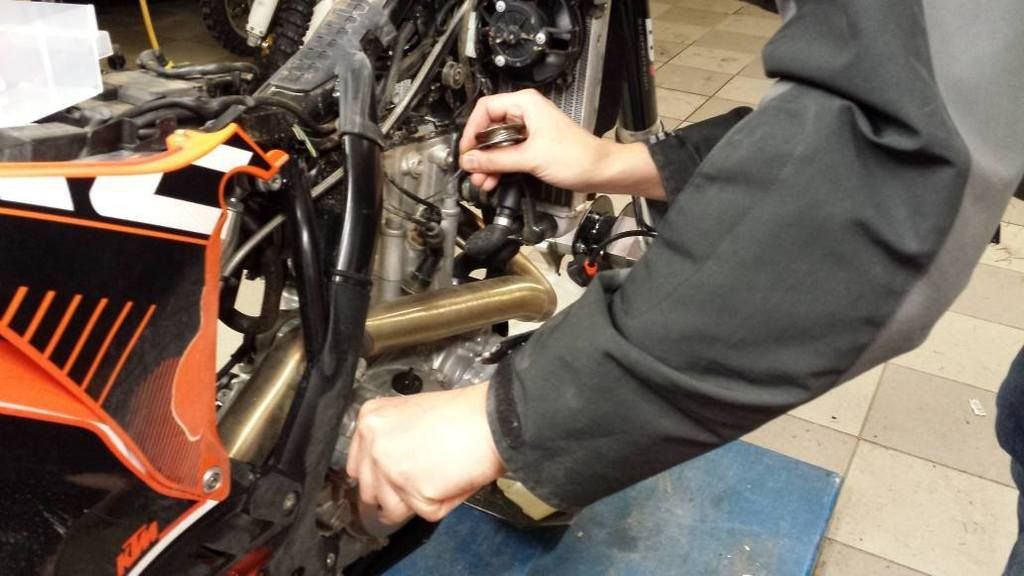
to be continued.....
<!-- / message --><!-- edit note -->